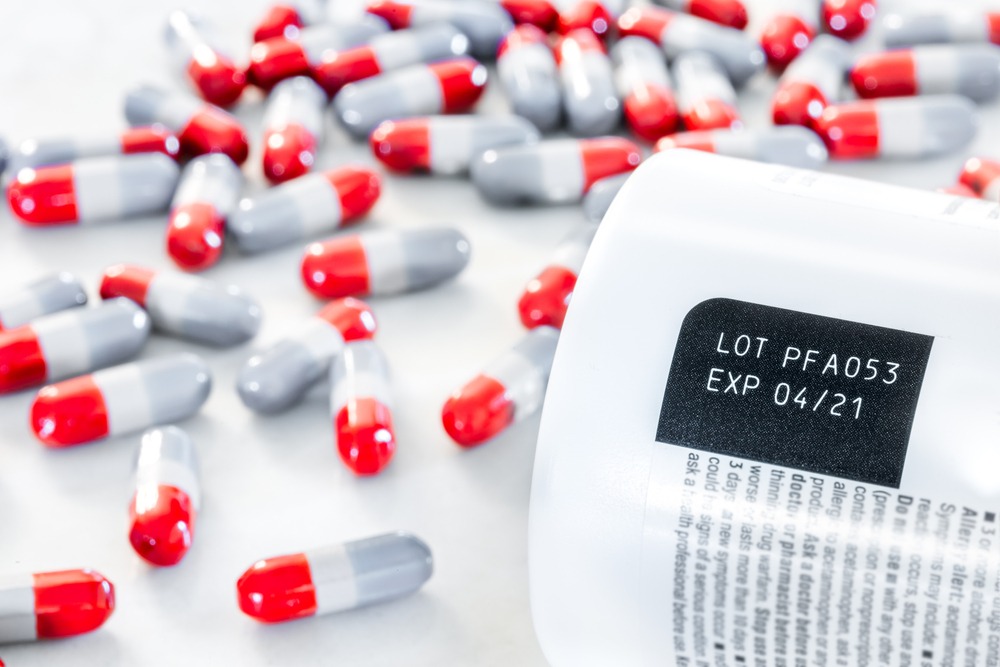
Global Pharmaceutical Company Develops Regulatory Labeling Quality Support Strategy
KEY BENEFITS
Enabled best practices in quality for regulatory labeling.
Delineated current state processes, systems pain points, and areas of opportunity.
Assessed best practices for managing documentation and training.
SOLUTION
Regulatory Management
INDSUTRY
Pharmaceutical
Overview
Pharmaceutical labeling is a highly regulated, complex process that must be operating efficiently to guarantee quality and safety. However, businesses frequently struggle with compliance difficulties, particularly when they are involved in international marketing. This is a major concern for the corporation and a problem with the regulatory bodies.
The major impact to the organization due to labeling issues could be a partial or complete market withdrawal or a huge penalty from the health authorities due to data inconsistency with the reference label data. This further creates ongoing challenges for organization as the processes are scrutinized by the regulatory authorities.
Companies may lose a huge amount of revenue and time towards product approvals and renewals. Given this situation, it is critical for organizations to ensure their submission processes are solid. Regulatory Information Management Systems/Software, or RIMS, are platforms that have emerged to assist pharmaceutical companies in submitting products for regulatory review.
In this case study, we discuss how a global pharma company leveraged Astrix’s expertise to:
- Enable best practices in quality for regulatory labeling.
- Delineate current state processes, systems pain points, and areas of opportunity.
- Assess best practices for managing documentation and training.
- Develop a future state, end-to-end regulatory labeling management strategy.
Business Challenges
A global pharma company was looking to improve their regulatory labeling process through migration to the existing Veeva RIM solution which would allow the labeling team to work more seamlessly and efficiently with adjacent Regulatory teams. Additionally, they were finding that their current operations for labeling quality documentation often included unclear roles and responsibilities, complex documentation, and overall, lacked visibility leading to global differences in policies and confusion within the labeling organization. They chose to take a deep-dive look at their systems, process, and policies in order to identify gaps and define a path forward for addressing these detriments.
The specific stakeholders involved with Astrix included, the organizations’ Regulatory IT, Labeling Global Regulatory Affairs groups in North America, the EU, and Internationally. Additional stakeholders from CMC, Supply Chain, and Global Packaging groups were consulted to enable enterprise-wide best practices. From a technology perspective, the project involved the existing Veeva Vault RIM System, their Legacy Labeling System, the Artwork Management, ERP, and other In-house Developed Systems.
How Astrix Enabled Success
Astrix worked closely with the client’s stakeholders to the Assess current regulatory labeling technical environment and processes to identify issues, gaps, and opportunities. From there, Astrix explored best practices with similar regulatory labeling teams through roundtable discussions with peer pharmaceutical companies and interviews with internal stakeholder groups. Astrix team worked closely with client teams to define the future state process, technology needs, and best practices for executing regulatory labeling and for managing associated processes, documentation, training, and communications.
Working closely with the client, Astrix defined and prioritized projects to:
- Create a roadmap outlining the path to implement new end-to-end processes and technology for quality documentation
- Define future state processes, integration points, configurations, and enhancements needed to incorporate labeling submissions into the existing RIM system.
How Astrix Made An Impact
The benefits achieved by this Global Pharma organization through this project included:
- Defined the current and future state business processes, including impacts to business processes, risks, and mitigations to support transition to Veeva Vault RIM solution.
- Developed use cases to drive configuration sessions to identify configuration needs and product enhancements for labeling authoring, planning, and tracking.
- Managed sessions, including facilitation of discussions, tracking of configuration items and enhancements, summarization of findings in sprint readouts and prioritization of use cases throughout Sprint sessions.
- Defined Release Plans to support implementation of labeling capabilities within the client’s Veeva RIM solution.
- Defined an end-to-end workflow management approach to standardize work process, documentation, training, and communication.
- Defined an approach to increase the ability to utilize relevant documentation and training. Reduce time associated with labeling work processes and on-boarding.
- Developed a multi-year implementation roadmap that is integrated with the technology roadmap to align to organizational priorities.
LET´S GET STARTED
Contact us today and let’s begin working on a solution for your most complex strategy, technology and staffing challenges.
CONTACT US