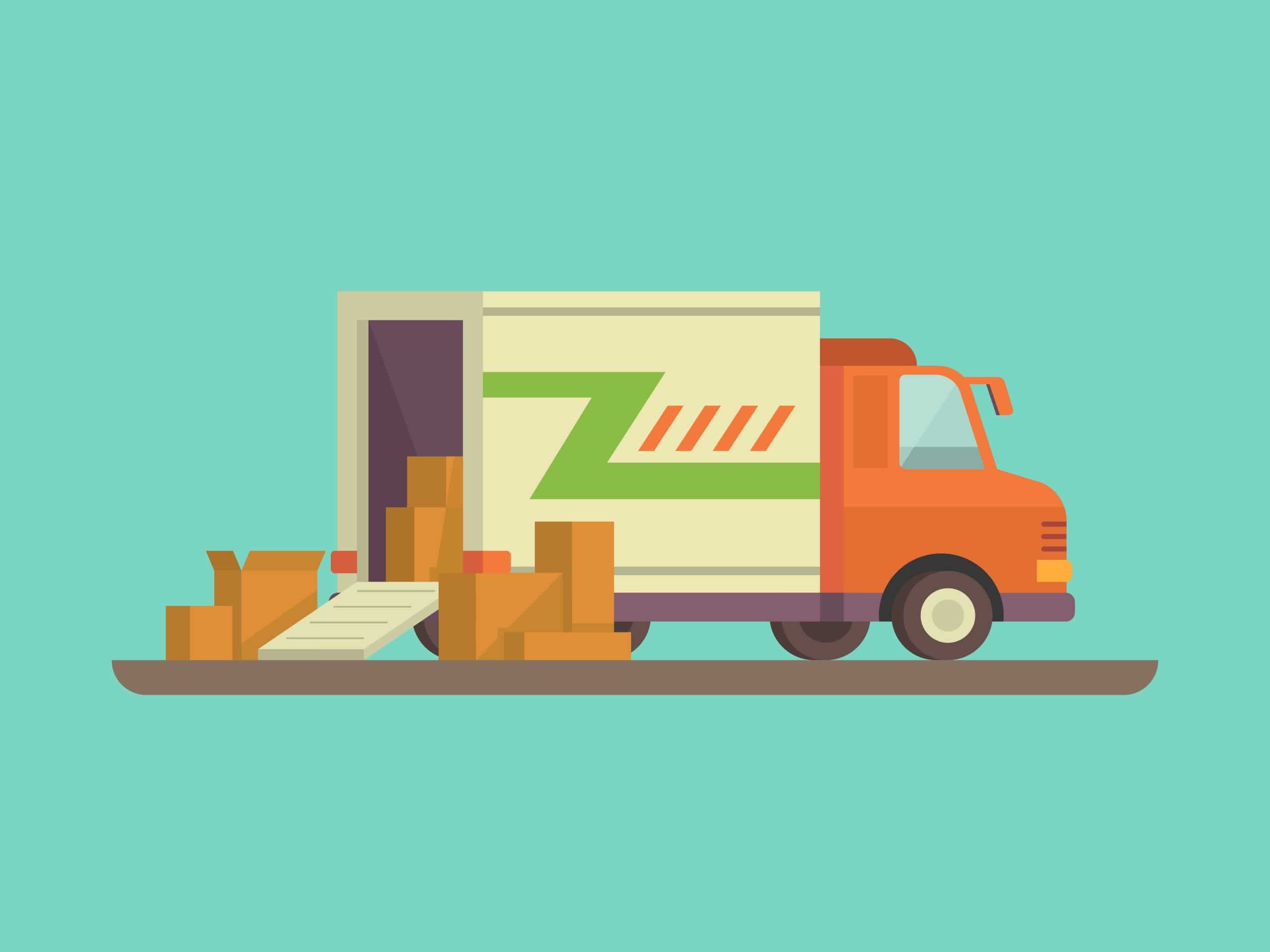
Laboratory Relocation Best Practices
The pace of change in the pharmaceutical and biotech industries means that most companies eventually must face the daunting task of relocating their laboratories. Whether due to mergers, acquisitions, funding changes or simply organic growth, a laboratory relocation is an extraordinarily complex undertaking that will impact your laboratory’s scientists, research and business goals.
A laboratory relocation involves moving high-end analytical instrumentation, hazardous materials, products and samples, and sometimes even live animals. It will require shutting down laboratory equipment, along with safely packing and shipping instruments, samples, materials, devices, computer hardware and potentially data to the new location. Once all necessary items have been moved to the new location, they will need to be unpacked and equipment will need to be requalification and/or validated.
Whether you are moving your lab across the hall, street or country, a laboratory relocation is never a routine exercise. The reality is that no two laboratories are alike – each will have a set of unique challenges that will need to be addressed with care. In this blog, we will discuss critical best practices that should be followed in all cases in order to make sure your laboratory relocation is a smooth, safe and efficient process that minimizes downtime and disruption for your business.
Best Practices for Laboratory Relocation
While a successful laboratory relocation can serve as a catalyst for company growth and enhanced innovation, a poorly managed relocation can be a disaster for your organization. Potential ways in which this “disaster” can unfold include:
- Failure to preserve the integrity of ongoing research
- Significant delays in ongoing research
- Damage to sensitive equipment
- Excessive costs to complete the move
Relocating your laboratory(s) can be an extremely complicated process. As such, there are a number of best practice recommendations that are important to follow to make your move go smoothly, some of which include:
Conduct a Site Assessment. It is important for the relocation team to meet with the lab manager to understand the background of the relocation, the nature of research being conducted, and any other important issues that need to be considered. A thorough assessment of both the old and new facilities should be conducted that includes the following:
- Complete asset inventory including all instruments, PCs, etc. Each instrument’s location, configuration, operational condition, and usage should be documented.
- Confirm needs of temperature sensitive chemicals, biological samples, and supplies
- Determine permits required for hazardous materials
- Record additional assets to be relocated including tables, hoods, chairs, etc.
- Map physical layout of the old and new facilities – include loading dock access schedules
Create a Detailed Plan and Schedule. A typical laboratory relocation can take three to six months of planning before a single piece of equipment is moved. When relocating a laboratory, having a plan that considers every detail is critical, particularly if you are moving more than one site. Once the scope of work is established, a project plan should be developed that includes every operational aspect of the move complete with timetables, ownership and logistics. The plan should coordinate sending and receiving facilities, provide a detailed schedule, identify and prioritize critical assets, detail asset placement in the new space, describe anticipated logistical obstacles and contingencies, include a risk management plan, identify any important transportation requirements, etc. Be sure to allow enough time to create the plan that will accurately capture all of your laboratory’s requirements. Once created, have all involved review and approve the plan.
Project Management Expertise. Laboratory relocation requires ongoing monitoring and reassessment. Even the best internal teams will struggle to anticipate every conceivable complication. An experienced project manager (PM) is therefore critical to ensure good coordination and communication. In addition to facilitating good communication, the PM will need to organize, track and report on the various steps of the lab move.
Communication Plan. Just a few of the many different types of details that will need to be communicated include:
- Scientists will need to know the date their equipment will no longer be available
- Decision-makers need to know how long it takes to decommission certain equipment
- Site managers need to know when their loading docks will be accessed
- Operations people will need to have a detailed overall assessment of the project
Develop a communication plan that involves all stakeholders to avoid disconnects between scientists, lab managers, management, facility managers, instrument vendors, and the people executing the move. Be sure to have a kick-off meeting with all involved and conduct weekly meetings to ensure everyone stays on the same page.
Build the Right Internal Team. It is important that you identify and include all the key stakeholders from your company that will need to be involved (e.g., site managers, financial/budget managers, EH&S, scientists, key decision makers, etc.). Additionally, if your move is over a long distance, you will need duplicate teams at both ends of the project.
Regulatory Compliance. An important consideration for any lab relocation is making sure all transport regulations are met. Depending on the types of material involved, along with the old and new destination, the project team may need to align with EPA, OSHA, DOT, FDA, and IATA regulations. Local and facility regulations may also need to be adhered to. In heavily regulated environments, such as pharmaceutical manufacturing and testing, movers must also comply with GLP/GMP guidelines. In this case, appropriate documentation should be maintained before, during and after the move.
Chain of Custody. Make sure you have a chain of custody in place for every piece of equipment, product or sample that you are moving so you know who is responsible for an item as it is going through the move process. This is especially important if you will be utilizing multiple vendors in the move.
Conclusion
The future productivity and profitability of your organization is impacted by the ability to execute a laboratory relocation successfully. That said, a lab relocation is a set of complex, interconnected activities that requires careful and detailed planning, efficient harmonization, proper execution, all within strict timelines and production schedules. While managing a lab demands its own set of skills, responsibilities, and knowledge, overseeing the intricate inner workings of relocation is typically not an internal core competency. In addition, most laboratory personnel assigned to a relocation typically already have full time jobs, which only increases the chance that important details will be overlooked.
If you don’t have personnel with the required skills and experience, it’s important to hire a third-party professional that does. A standard relocation company is not ideal, however, as not all project or facilities management companies are experienced in laboratory relocations. Ideally, you want a company who understands the Life Science industry and specializes in laboratory logistics. Your mover should understand the laboratory environment and instrumentation, have project management expertise, inventory management expertise, and field service engineering expertise. Hiring a qualified lab mover mitigates risk, improves efficiency, saves money, and enables scientists and lab staff to focus on their research.
Case Study: LabWare Centralized Data Review for a Global Biopharmaceutical Company
Overview A global biopharmaceutical company specializing in discovery, development,... LEARN MOREWhite Paper: Managing Data Integrity in FDA-Regulated labs.
New White Paper LEARN MORELET´S GET STARTED
Contact us today and let’s begin working on a solution for your most complex strategy, technology and staffing challenges.
CONTACT US