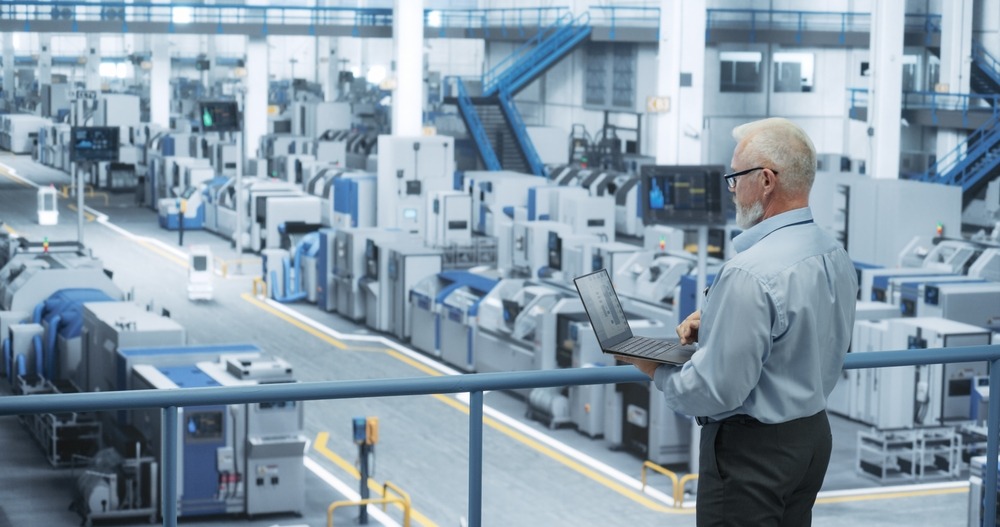
Astrix Partner Blog – Quality 4.0: The Manufacturing Movement’s Impact on Lab Operations
Astrix works with thought leaders throughout the Life Science industry. This includes a variety of technology partners with whom we collaborate on projects and industry thought leadership. As part of this we feature high quality content from our partners to help our customers and website visitors learn about new technologies, process and strategy that may help move their R&D operations through a digital transformation!
Featured Blog from STARLIMS
Are We In the 4th Industrial Revolution?
If you’ve been paying attention to the rapid pace of technological advancement, you might wonder: Are we in the 4th Industrial Revolution? According to many experts the answer is a resounding “yes!” The industrial revolutions of the past 300 years have served as markers of significant shifts in how our world operates, each one pushing us toward new modes of economic growth and societal transformation. Let’s take a quick journey through these industrial eras.
A Brief Timeline of the Industrial Revolutions
- Industry 1.0: The late 1700s to early 1800s saw the rise of steam engines, power looms, and other machinery that began to replace manual labor. This era marked the birth of industrialization as we know it.
- Industry 2.0: Spanning from 1870 to 1914, the Second Industrial Revolution was driven by electricity and brought about rapid scientific discovery, standardization, and the dawn of mass production.
- Industry 3.0: From 1947 to the early 2000s, the world transitioned into the Information Age, also known as the Computer Age or the Digital Revolution. This period was characterized by the shift from analog to digital technology and the rise of high-powered computing systems.
Each of these revolutions led to massive changes in how we produce goods, laying the groundwork for the modern manufacturing processes that drive today’s economies. As our methods of production evolved, so did our approach to quality—a key aspect that has remained central to industrial success. In this blog, we’ll discuss Industry 4.0, Quality 4.0 and how they impact quality activities within a manufacturing environment and how you, too, can be active in Quality 4.0.
What is Industry 4.0?
Welcome to Industry 4.0—also known as the Fourth Industrial Revolution or 4IR! This revolution is all about the digital transformation sweeping through industrial organizations, powered by emerging technologies that you are likely already familiar with: big data analytics, cloud computing, artificial intelligence (AI), the Internet of Things (IoT), blockchain, 3D printing, and more.
While the pace of technological advancement has accelerated over the past three decades, the term “Industry 4.0” only gained traction in the last decade. It encapsulates the shift toward hyperconnected, tech-enabled organizations that prioritize efficiency, growth, and productivity through advanced digital solutions.
How Does Industry 4.0 Impact Quality?
In each phase of the Industrial Revolution, manufacturers have had to adjust their quality activities alongside evolving technology. As industries integrated more machinery and equipment into production processes, quality took on a more critical and central role.
A Brief Timeline of the Evolution of Quality Manufacturing
- Quality 1.0: During Industry 1.0, the priority for manufacturers was the scaling-up the volume of production. Quality was primarily measured through physical self-inspection.
- Quality 2.0: As manufacturers became reliant on electrically powered machines, they implemented measures to oversee quality and safety of both marketable goods and equipment.
- Quality 3.0: In this phase, more emphasis began to be placed on customer satisfaction and the creation of standardized protocols that could be implemented across the organization.
What is Quality 4.0?
This brings us to modern times, with Quality 4.0. An extension of Industry 4.0, Quality 4.0 refers to this new digital paradigm as it impacts quality activities within manufacturing. Organizations committed to Quality 4.0 are mobilizing new Industry 4.0 technologies to improve quality management and operational excellence while lowering costs, simplifying compliance, and driving efficiencies—all while maintaining high standards of quality.
The Benefits of Quality 4.0 Technology
By investing in Quality 4.0 technology, manufacturing organizations get a number of benefits. In prioritizing data capture at the onset, organizations gain a greater visibility into their workflows, allowing them to maintain a complete audit trail that simplifies audits and compliance efforts. With access to real-time data and analytics, organizations can make better decisions faster, and even forecast the future with predictive analytics. This empowers organizations to adapt quickly to changing conditions and creates a culture of ongoing improvement.
To summarize, Quality 4.0 technology enables your organization to…
- Augment and support human intelligence
- Accelerate and enhance decision-making
- Boost transparency, traceability, and auditability
- Anticipate changes and adapt
- Evolve toward continuous improvement
Quality 4.0 In the Laboratory
The technological advancements that have been made during Quality 4.0 have unlocked capabilities in the lab that decades ago would have been unimaginable. The impact Quality 4.0 technology can have on lab operations cannot be overstated. Solutions like laboratory information management systems (LIMS) provide secure, centralized data capture and oversight as well as automation capabilities.
What is STARLIMS?
Case Study: LabWare Centralized Data Review for a Global Biopharmaceutical Company
Overview A global biopharmaceutical company specializing in discovery, development,... LEARN MOREWhite Paper: Managing Data Integrity in FDA-Regulated labs.
New White Paper LEARN MORELET´S GET STARTED
Contact us today and let’s begin working on a solution for your most complex strategy, technology and staffing challenges.
CONTACT US